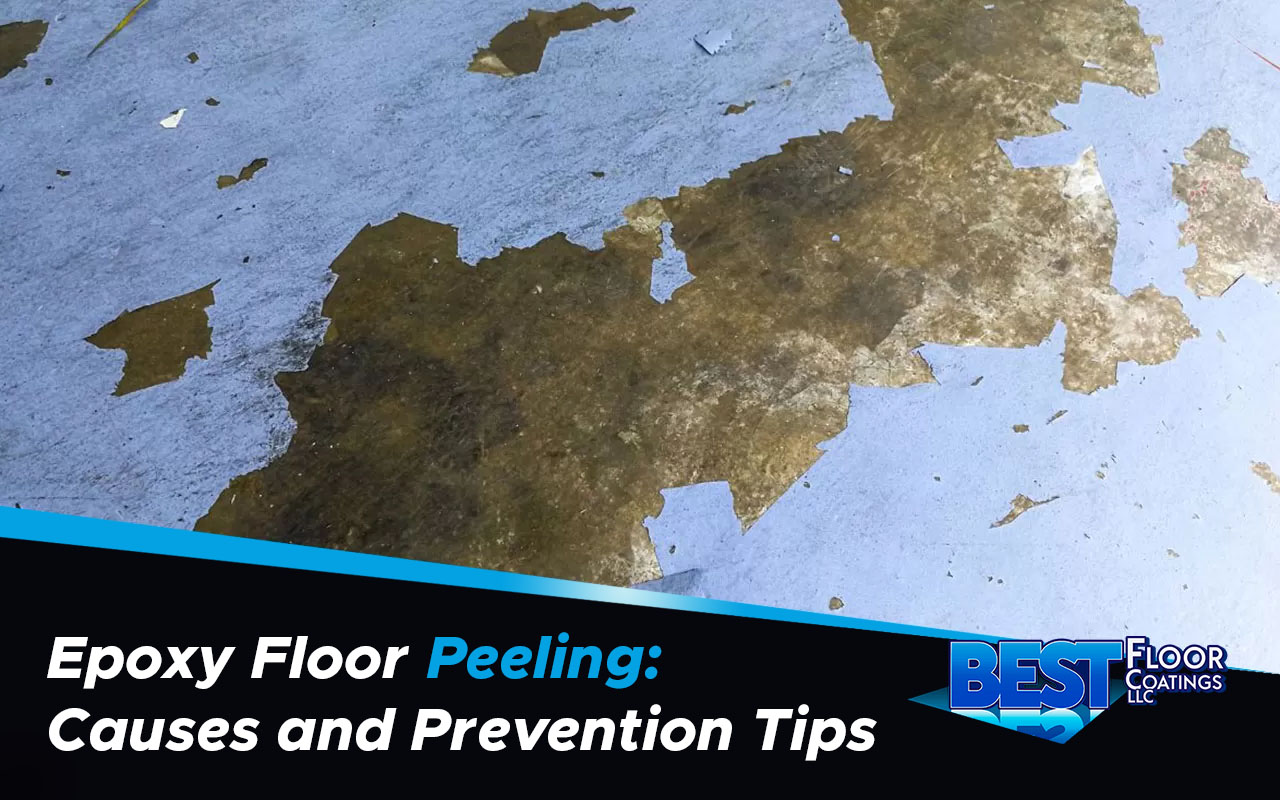
In this Article:
Epoxy Floor Peeling – Causes and How to Avoid It
Follow Epoxy Mixing and Application Guidelines
Additional Information Just For You
Additional Tips for Preventing Epoxy Floor Peeling
Fascinating Epoxy Flooring Facts
Trust Best Floor Coatings LLC for Long-Lasting Epoxy Solutions
When it comes to maintaining a sleek and durable surface, few options match the appeal of an epoxy coating. However, you want to know about epoxy floor peeling, its causes, and how to avoid it is a critical topic for homeowners and businesses who value their flooring investment. Peeling epoxy floors not only tarnishes the look of your space but can also signify deeper issues at play.
We will uncover the various factors that can lead to the disappointing sight of a peeling epoxy floor and explore the preventive measures you can take to ensure your floor remains immaculate and enduring. Join us as we delve into the reasons behind epoxy floor degradation and learn how to preserve the luster and longevity of your flooring.
Epoxy Floor Peeling – Causes and How to Avoid It
To ensure the longevity and aesthetic appeal of your epoxy floors. It is crucial to understand why peeling occurs and how to prevent it. Let’s dive into the main causes of epoxy floor peeling and follow up with targeted prevention tips.
Causes of Epoxy Floor Peeling
Inadequate Surface Preparation
Cause: A clean, porous surface is essential for epoxy to adhere properly. Residual dirt, oils, paint, or other contaminants can create a barrier, causing the epoxy to peel over time.
Prevention Tip: Begin by thoroughly cleaning the surface using a degreaser to remove any oils or grease. Then, employ mechanical methods like grinding or shot blasting to open up the concrete’s pores and ensure a strong bond. After grinding, use a vacuum to clear dust and debris. Make sure the floor is fully dry and free of contaminants before applying the epoxy.
Moisture Issues
Cause: Moisture trapped in or below the concrete can interfere with the curing process, causing the epoxy to lift and peel.
Prevention Tip: Conduct a moisture test, such as a calcium chloride test, or use a moisture meter to determine the moisture level in the concrete. If the reading indicates high moisture, consider applying a vapor barrier or a moisture-tolerant primer before the epoxy application. In high-humidity areas, run a dehumidifier to reduce moisture in the environment both before and during application.
Improper Mixing or Application
Cause: Epoxy requires precise ratios and specific temperature conditions to cure correctly. Improper mixing or applying epoxy at the wrong temperature can lead to peeling and weak adhesion.
Prevention Tip: Always follow the manufacturer’s instructions to the letter. Mix the components thoroughly and in the correct proportions to ensure a proper cure. Temperature is also critical—apply the epoxy in a controlled environment where the temperature stays between 60°F and 90°F for optimal curing. A thermometer is used to monitor the floor and room temperature before and during application.
Quality Materials: Invest in Long-Lasting Epoxy Flooring
When it comes to epoxy flooring, quality materials make a significant difference in both performance and longevity. Cheap epoxy products may seem appealing at first due to their lower cost, but they often lack the durability and resistance that premium products provide. Here’s how investing in high-quality epoxy materials can prevent peeling and ensure your floors stay in top condition:
UV Resistance
Why It Matters: UV rays can cause some epoxy coatings to yellow, fade, or weaken over time, particularly in areas with natural sunlight. Inferior epoxy products may lack UV stabilizers, leading to faster degradation and peeling.
Prevention Tip: Choose an epoxy product with UV-resistant properties, especially for areas exposed to sunlight. High-quality epoxies contain UV stabilizers that reduce the risk of discoloration and preserve the floor’s appearance for years.
Chemical and Abrasion Resistance
Why It Matters: Epoxy floors are often exposed to chemicals, oils, and heavy foot or vehicle traffic. Lower-grade epoxies may not be designed to handle these conditions, resulting in peeling, scratches, and damage over time.
Prevention Tip: Look for high-grade, industrial-strength epoxies that offer superior chemical and abrasion resistance. These are particularly valuable for garages, workshops, or industrial spaces. High-quality coatings can resist spills and withstand impact, which keeps the surface intact and peeling-free.
Thickness and Build Quality
Why It Matters: High-quality epoxy products typically provide a thicker, more substantial coating compared to cheaper alternatives. Thin, low-grade coatings may not adhere well, especially if applied to surfaces that encounter high traffic or heavy equipment.
Prevention Tip: Opt for epoxies with higher build quality or those labeled as “100% solids epoxy,” which means the product is composed entirely of epoxy without additional fillers. This results in a thicker, stronger coating that is less likely to peel or wear out over time.
Moisture Tolerance
Why It Matters: Moisture can be particularly problematic for epoxy floors, especially in humid climates or on concrete that may still contain residual moisture. Quality epoxy products are often formulated with better moisture tolerance, reducing the risk of peeling caused by moisture issues.
Prevention Tip: When working in moisture-prone areas, select an epoxy with moisture-tolerant properties or pair it with a moisture-blocking primer to improve adhesion. This investment in quality materials minimizes the risk of peeling due to moisture infiltration.
Application Flexibility and Longevity
Why It Matters: Premium epoxy products are engineered for easier application, better curing, and greater durability over time. Lower-quality options may require more specific conditions to apply and may not cure evenly, leading to future peeling issues.
Prevention Tip: Invest in a reputable epoxy brand that is known for flexibility in application and longevity. High-quality brands often have warranties or guarantees, providing assurance of a durable finish. When paired with proper surface preparation and application, these products can extend the life of your flooring by a decade or more without peeling.
Follow Epoxy Mixing and Application Guidelines
Always adhere to the manufacturer’s instructions when mixing and applying epoxy. Ensure that the components are mixed thoroughly to the correct ratio and that the application is performed within the suitable temperature range. This meticulous approach will promote optimal curing and adhesion, significantly reducing the likelihood of peeling.
By addressing these causes and adhering to these prevention tips, you can significantly enhance the durability and appearance of your epoxy flooring.
Additional Information Just For You
Here are additional tips, facts, and common questions to assist you in maintaining the integrity of your epoxy flooring.
Additional Tips for Preventing Epoxy Floor Peeling
Climate Control: Maintain a consistent temperature within the space where the epoxy is applied, not just during the application but also through the curing process.
Quality Materials: Invest in high-quality epoxy products. The market is flooded with varieties of epoxy, and not all are created equal. High-quality materials may cost more upfront but can prevent peeling and other issues in the long run.
Professional Assessment: Before application, have a professional assess your floor. They can identify potential issues that may not be obvious to the untrained eye.
Fascinating Epoxy Flooring Facts
Versatility: Epoxy flooring is for more than just garages or industrial settings. It’s also perfect for residential spaces, offering various finishes and colors.
Hygienic: Epoxy floors are seamless and resist liquids, making them an excellent choice for areas requiring sterile conditions, like hospitals or food preparation spaces.
Green Option: Epoxy flooring is a green option since it reduces the need for new materials and can be applied directly over an existing substrate.
Frequently Asked Questions
Q: Can you repair peeling epoxy floors?
A: Yes, peeling epoxy can often be repaired. The affected area needs to be removed, the underlying surface prepared again, and a new coat of epoxy applied.
Q: How long does an epoxy floor last before it starts peeling?
A: A well-applied epoxy floor can last ten years or more without peeling, depending on use and maintenance.
Q: Are there any signs that epoxy might start peeling soon?
A: Bubbles, discoloration, or a tacky surface might indicate issues with the epoxy bond that could lead to peeling.
By taking these additional measures and considering the facts and answers to common concerns, you can better safeguard your epoxy floors against peeling and ensure a lasting, attractive surface.
Trust Best Floor Coatings LLC for Long-Lasting Epoxy Solutions
At Best Floor Coatings LLC, we understand that the key to a long-lasting and beautiful floor lies in the quality of both the products used and the expertise of the application. Our professional services are designed to address the common issues of epoxy floor peeling, ensuring that each project we undertake is equipped to stand the test of time.
Whether you’re facing current peeling issues or looking to install a new epoxy floor, trust Best Floor Coatings LLC to provide a solution that merges aesthetic appeal with unparalleled durability. Our team of experts is dedicated to transforming your space with an epoxy flooring system.
Don’t let epoxy floor peeling disrupt the beauty and functionality of your space. Contact Best Floor Coatings LLC today to ensure a flawless and enduring finish for your floors!